Armed with innovative ideas, products and services, we offer smart solutions to the significant issues of today and tomorrow. The built environment is becoming increasingly interactive thanks to intelligent systems that generate data, providing us with information that helps us serve our clients even more effectively. We are also taking big steps to become smarter in the construction process itself, including standardisation and the use of industrialised processes. Heijmans’ ambition is to (continue to) play a leading role in the design, realisation and management of the built environment, and we therefore want to help make the chain smarter to increase its impact and effectiveness.
9. All the projects we work on will have a digital twin in 2023.
Non-residential Building
Heijmans Non-residential Building business is building on its work with so-called digital twins. Our new-build projects are all produced using a high-quality BIM model (see also appendix 11.6.14). In recent years, the focus has been on increasing the integration of our work with BIM models into our work processes. Our designers, work planners and contractors now work on a daily basis with the 3D geometric models and information from the BIM models to ensure the optimal coordination, preparation and execution of our projects. Of the 25 BIM goals to be achieved on our roadmap (BIM ambition ladder), we are currently applying more than 20 on a regular basis in our projects, plus we have documented best practices for these. Applying BIM (in every layer of the organisation) is now an operational matter and no longer a strategic improvement. This is how commonplace working with BIM has now become.
Renovation of the Binnenhof
The preparations for the renovation of the Dutch houses of parliament, the Binnenhof, included the making of an extensive 3D model. Because although Heijmans is doing part of the job with the renovation of the Senate and Council of State, all the construction firms involved have to coordinate their work down to the smallest details. This digital model enables all the companies involved to work together faster and more efficiently and to check whether their work can be carried out safely and according to plan. When renovating listed buildings, you often come across a few surprises: for instance, a medieval staircase was found during the foundation research. This too is now included in the 3D model. So in effect, the 3D picture becomes more and more complete as the project progresses.
We offer so-called 'paint shop and car wash' training courses for all job groups on a regular basis. In these training courses, our employees learn the basics of working with BIM models (paint shop) and are regularly provided with the latest insights (car wash).
One of the new developments in 2022 was our use of pointclouds (a way of measuring a building) for progress monitoring and quality control. This involves placing a tripod with a spinning operator on a spot. On each full turn, the operator shoots measurement points into space, which are then fed back digitally. After tens of millions of rotations, this creates a pointcloud that represents what a space looks like. The knowledge and expertise in this field will be available for deployment on projects in 2023.
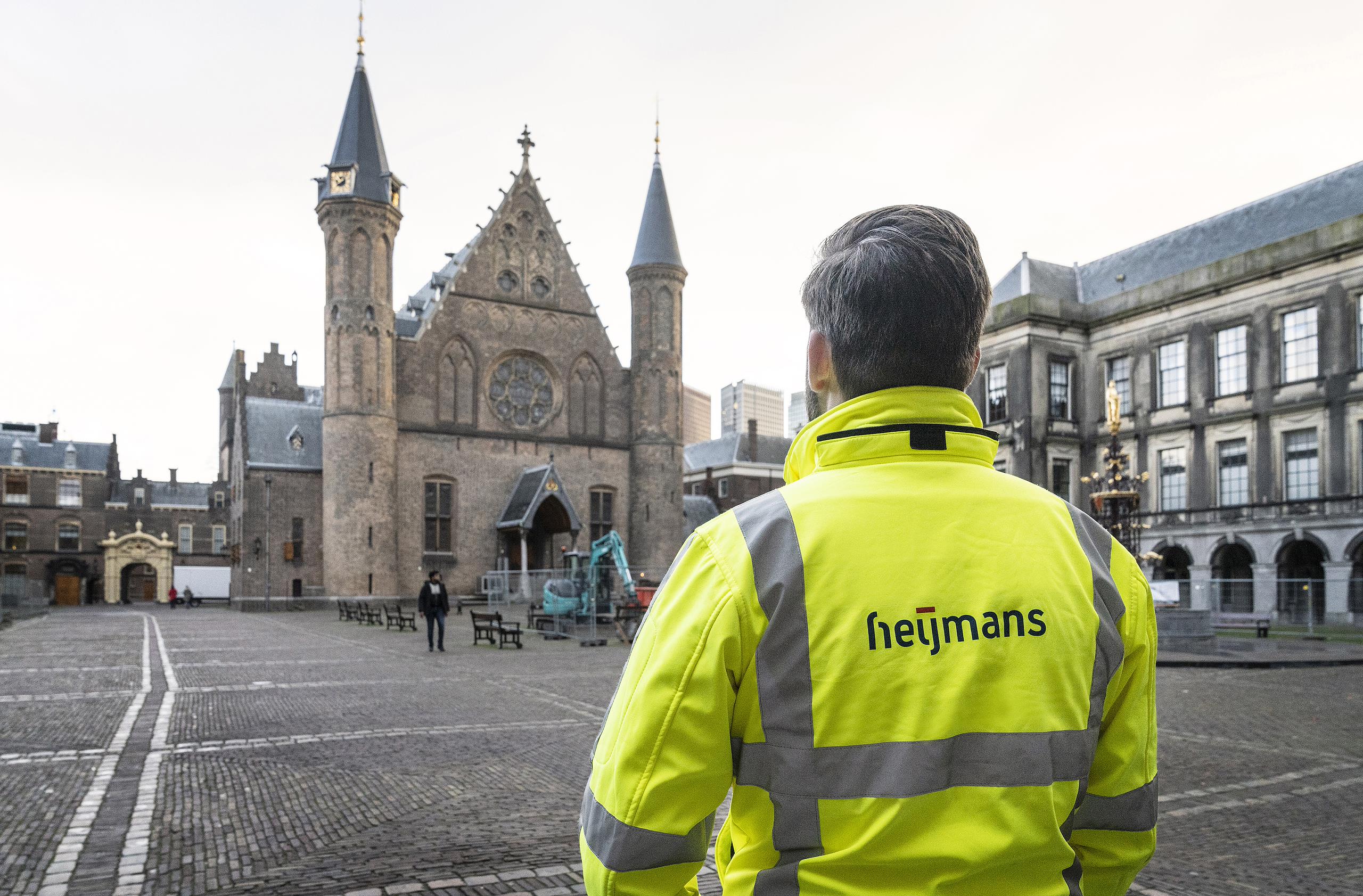
For our maintenance contracts, we are working with a digital twin proposition called DreAM. This application is based on a 3D BIM model, which delivers information relevant to maintenance and management processes. By combining substantive professional know-how about construction and maintenance and data sources on our own processes and building use (sensor data), we are generating new insights that we would not have without the digital twin (DreAM). In 2022, we created and commissioned two Proofs of Concept in this field. In 2023, we will expand this into a Minimal Viable Product that we can deploy on more projects.
Residential Building
At Residential Building, we are currently seeing an upward trend in the average number of BIM stars achieved per project. This is the main indicator of the fact that we are taking a structured approach to all projects using the BIM Focus Project approach. And more importantly, this is delivering results. Not only in terms of the number of BIM stars achieved (divided over five levels), but also in terms of the perception of the people on the projects and the financial results on those projects. Projects run more smoothy and in a more structured way, resulting in more streamlined processes and lower failure costs.
Together with TNO, we have developed a reference architecture based on existing, reusable architecture. This gives us a template, so to speak, we can use to develop a complete digital twin step-by-step across the entire lifecycle of a home. We can do this both for the production process of our timber-frame houses at the Heerenveen factory and for the Horizon house itself. We are also working on a new digital home configurator, which buyers can use to customise their own new-build homes. This home configurator will be integrated in the manufacturing software to provide a continuous flow of information.
Infra
We use a digital twin in all infra projects, both new-build and management and maintenance. This starts with setting up a geographical information model, which serves as the central information point for our colleagues.
In our new-build assignments, we use BIM targets (‘stars’) with different ambitions depending on the complexity of the projects. For the most complex Infra projects in 2022, we achieved our high ambition of eighteen stars. These include the Gorinchem - Waardenburg and Sterke Lekdijken dyke reinforcement projects, the projects on the take-off and landing runways at Schiphol Airport, the renovation of the Piet Hein Tunnel and the Apeldoorn - Twello stretch of the A1 motorway.
We have seen a particularly big increase in the use of BIM in energy transition-related projects, including those for our client TenneT or our civil engineering projects, including through the application of best practices for complex projects. So the use of digital twins is now widely embedded in the organisation.
In 2022, we took a number of significant steps in the continued development of our best practices. One of these is the standard exchange between geographic (GIS) data and the 3D BIM model. This enables our colleagues to find the most relevant project information quickly and clearly in a user-friendly way, both in the office and at the project site. In line with our goal to unlock key project information, we also saw the simulation of the construction process (4D BIM) really take off in 2022. This clear-cut way of working, in which planning, the current situation and the intended situation are all aligned, gives those involved from design, work preparation and realisation a verified picture of how to do the work. This contributes to safer execution and lower failure costs.
In addition, we took a number of significant steps to automate and parameterise the design process. For instance, in terms of automatically generating 2D drawings and building new design apps that largely take care of part of the design process.
For Infra, good subsurface mapping is crucial to prevent excavation damage. To this end, we have some key innovative technologies in place that can map the subsurface very accurately. For instance, Infra conducted a pilot for the visualisation of the underground 3D model of a planned new sewer system using Augmented Reality. This 3D model was visualised in the existing subsurface to directly map the interaction with the existing cables and pipes. In 2022, we applied this technology to several underground projects after an initial pilot.
10. We successfully launch five new data-driven services in the market each year.
In addition to the continued development of propositions to create new products for our customers, for example by adding new value elements to existing products and services, we developed and launched a total of seventeen new data-driven services in the Building & Technology, Infra and Property development business areas. We briefly describe a number of examples below:
-
For example, we developed the data centre generator for data centre design. This enables parametric design of data centres based on a predefined catalogue of 36 building blocks and components. This service has already been included in several tenders, and clients have responded enthusiastically.
-
Data-driven sustainable advice includes insight into energy demand and consumption during project realisation, an emission dashboard for nitrogen, ammonia and CO2 and a material flow analysis. In addition, we standardised and automated the calculation of the Environmental Cost Indicator and Environmental Performance Building scores.
-
Iris 2.0 is the online service Heijmans Services uses to give its clients insight into the user value, property value and service value of their buildings and assets. The complete Iris dashboard, which combines information from multiple systems clearly and transparently, puts clients in control of their own assets. We have now implemented this solution at fifteen clients.
-
Our Insight product can be used for asset analysis by remotely retrieving data from buildings. For instance, Insight can analyse whether sun blinds are working properly by linking them to data on sun hours. Remote and proactive action can then be taken to make an improvement or adjustment, without disturbing the client’s primary process. We have now linked up 52 buildings and we have launched a similar project to remotely read out security systems. We expect these two trajectories to converge in 2023.
-
The Heijmans energy storage system is a smart energy storage system combined with energy management for utility projects, including a spin-off for the physical management and maintenance of systems. It provides an immediate solution to the acute energy transition problems our clients may face. The problems may differ per market/client situation. Talks are ongoing with the province of Overijssel and our timber-frame housing factory in Heerenveen to start using this system first.
-
The charging station scan provides insight into the possibilities for the installation of (additional) charging stations. This can also be used in combination with the supply of charging poles (infra) and the physical modification of a building’s energy installation, a standard part of Heijmans Energy Services’ product range.
-
For the monitoring of Dynamic Traffic Management (DVM) systems, such as matrix signs, cameras and dynamic route information panels (DRIPs), clients on two long-term management and maintenance contracts will have the ability to see and prioritise all failures in real time directly from all connected DVM assets.
-
In 2022, we continued the development of two traffic management services. For traffic management during large-scale road works, we developed the journey time monitoring service into a production-ready and therefore cybersecure solution. This service shows the expected and actual journey times in real time during diversions. This enables Heijmans to make immediate traffic management adjustments at these diversions, especially on the secondary road network. In addition, Infra has developed its Digital Road Safety System. In the context of safe working along and on roads, Heijmans has developed a system that allows colleagues to report their road works in real time to navigation software such as TomTom, Google and Waze via a box in the car. This notifies road users immediately if there are roadworks in their neighbourhood.
-
Heijmans Property Development deployed bi-directional charging in cooperation with a partner at Leidsche Rijn in Utrecht. This development is crucial to secure the energy balance of neighbourhoods in the future.
11. The number of subscriptions based on data-driven services in the in-use phase increases 50% each year.
At Building & Technology, the growth of Beyond Eyes services among its clients also developed nicely in 2022. For instance, the number of buildings using Beyond Eyes services increased by 49% to 330 buildings. The number of subscriptions increased by 13% to a total of 141 subscriptions, spread across 102 unique companies.
At the end of 2022, Beyond Eyes was also awarded ProRail’s definitive tender for ‘Workplace and space sensors’. The implementation of 4,500 sensors in seven different locations will start in early 2023. This will involve collecting data with the aim of creating an optimal workplace in the office and realising the efficient use of offices.
Recycling firm PreZero has now joined Heijmans and cleaning company CSU as Beyond Eyes’ third family member. With this move, Beyond Eyes has expanded its data-driven facilities services to include waste management. The addition of PreZero marks another big step in making organisations’ facilities processes more sustainable.
At Infra, five existing long-running subscriptions were extended for another three to four years. This underlines the importance of subscriptions for data-driven services in terms of generating long-term stable revenues. In addition, we gained six subscriptions for the five services mentioned above. Together with two ongoing services, this took the total number of subscriptions to 13 in 2022.
Property Development issued 573 subscriptions for its data-driven services to private buyers/users of a Heijmans property in 2022.
Key performance indicator |
Score 2022 |
Score 2021 |
9. All the projects we work on will have a digital twin in 2023. |
84%* |
71% |
10. New data-driven services launched succesfully |
17 |
9 |
11. The number of subscriptions for data-driven services in the in-use phase |
727 |
212 |
- *This percentage pertains to projects in the realisation phase.
12. In 2025, we have transferred 50% of our hours – compared with 2020 – from on-site to off-site.
The shift from on-site hours to off-site hours is a measure of our planned industrialisation and standardisation. This will enable us to achieve a number of objectives related to safety, sustainable employability, the quality of delivered products and the reduction of failure costs.
In 2022, on the Heijmans Woonconcept (concept houses - HWC) front, we remained in line with the numbers recorded in 2021, with 689 assembled shells. The absolute number is slightly lower, because we completed five pilot projects involving a total of 38 of our new Horizon concept homes (timber-frame houses). In addition, we also produced elements of homes for external clients.
We also made substantial progress with our stacked concepts (apartment blocks). For instance, in November we signed an agreement with the Kleurrijk Wonen housing corporation for the first 43 Huismerk apartments in Culemborg. This is our stacked concept with gallery access for the affordable (rental) market. A number of follow-up projects have now moved into the development phase, including projects in Arnhem and Culemborg. The Heijmans Apartment Concept with portico access for urban (redevelopment) areas is also moving towards development and realisation. With a broad palette of apartment types and floor plans, we can also give a conceptual interpretation to these projects, as we did in the south-western part of The Hague (Dreven, Gaarden, Zichten project), the Lodewijk van Deijssel neighbourhood in Amsterdam and Overvecht in Utrecht. By the end of 2022, 629 Heijmans Apartment Concept homes were under development.
For our concept homes, we use prefabricated components wherever possible, with these produced or assembled in the factories of our co-makers involved in the concepts. For both the houses and the stacked products (apartments), the shell, roof and (a large part of) the façade are supplied in prefabricated form for assembly at the building site. In addition, we constantly review which other components can be prefabricated; for example, we are running a pilot project for the Heijmans Woonconcept homes, including a ready-to-use floor (including installations ex-factory and with no finishing floor required ) and the use of prefabricated internal walls. In addition to the objectives mentioned above, this provides circular benefits as less material is needed, there is less waste and the internal walls are made of bio-based material instead of aerated concrete.
We also worked very hard in 2022 to prepare the factory we acquired for the production of Heijmans Horizon homes from 2023 onwards.
This means a growing part of our production is shifting from on-site to off-site, not only in terms of conceptual to industrial (in our own factory) but also for both houses and apartment buildings.
Key performance indicator |
Score 2022 |
Score 2021 |
12. Concept homes delivered |
776 |
613 |
Building for the future
The development of Heijmans’ latest generation of homes focused on a number of major issues. How can we make our operations more sustainable? How do we offer a solution for the enormous and growing shortage of affordable housing? And how do we achieve this in an efficient and safe way at a time when fewer and fewer skilled workers are available? The answer is Heijmans Horizon. Heijmans has years of experience with conceptual building together with co-makers. Industrialisation and standardisation combined with variation make it possible to build quickly and efficiently for numerous target groups. But we cannot realise our sustainability and innovation ambitions on our own. Which is why we looked for the right partners; to share knowledge, learn together and by doing so increase the number of sustainable and high-quality homes in the Netherlands both faster and smarter. We have all gained experience in the first few projects. From 2023, we will build these sustainable homes in our energy-neutral factory in Heerenveen. The industrialisation of standardised timber-frame construction is effectively a shift from engineering to configuration. What this means is that from 2023 customers will be able to put together their own timber-frame houses using the Heijmans 3D Residential Configurator. At home on their computer or tablet, and at their leisure.